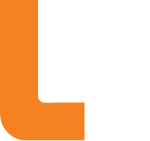
CONTACT

FAQ
Questions, answers
For optimization, we generally need two modules to create a single apartment. Therefore, the number required depends on the number of apartments you want. Additionally, there are modules available for common areas. Feel free to contact us for a feasibility study on your project.
Modular construction has certain constraints related to road transport. Standards allow modules to have a maximum width of 16′-0″ overall. However, transportation costs are reduced for modules that are less than 13’10”, and even more so for modules less than 12′-0″.
For depth, the ideal is 42′-0″, but we can go up to 46′-0″.
The height of the modules can vary from one floor to another. Ideally, a maximum height of 11′-3″ including floor, walls, and ceiling/roof is requested. We can still reach a height of 12′-0″ for some projects, but the route to your site requires validation with the transporter.
These are factors to consider during the design process and we can assist you in this process.
For depth, the ideal is 42′-0″, but we can go up to 46′-0″.
The height of the modules can vary from one floor to another. Ideally, a maximum height of 11′-3″ including floor, walls, and ceiling/roof is requested. We can still reach a height of 12′-0″ for some projects, but the route to your site requires validation with the transporter.
These are factors to consider during the design process and we can assist you in this process.
Locusi modules are transported by specialized trucks and trailers from our factory to your construction site or storage location. For deliveries to more remote areas, most modules are transported by truck, but some of our modules can also be transported by train and by boat.
On the day before or the day of installation, a crane is set up near the future building site. The foundation must be prefilled and leveled by your excavation subcontractor. The modules are then moved close to the crane by a specialized trailer and unpacked by another team. The crane operators and the installation team work quickly to assemble and anchor the building. Depending on the project specifics, the site, and the weather, installation can vary between 8 and 15 modules per day.
Installation is done vertically, from the first level up to the roof, which allows for better waterproofing in case of rain if the installation extends over several days.
Modular connections continue for a few days after the final assembly of the building. Your subcontractors can still work in parallel with these tasks once the first phase is erected.
To deliver a complete and hassle-free product, we can handle the installation, modular connections, crane rental, machinery, anchoring, and all materials necessary for the building’s waterproofing. When we leave your site, your building is sealed and ready for mechanical and finishing work.
If you have multiple projects and want to employ your workforce, we can also provide training for installation and/or modular connections.
Installation is done vertically, from the first level up to the roof, which allows for better waterproofing in case of rain if the installation extends over several days.
Modular connections continue for a few days after the final assembly of the building. Your subcontractors can still work in parallel with these tasks once the first phase is erected.
To deliver a complete and hassle-free product, we can handle the installation, modular connections, crane rental, machinery, anchoring, and all materials necessary for the building’s waterproofing. When we leave your site, your building is sealed and ready for mechanical and finishing work.
If you have multiple projects and want to employ your workforce, we can also provide training for installation and/or modular connections.
The ideal solutions are:
- To build all your modules in advance. For example, during the winter or alongside your excavation and foundation work.
- To have a sufficiently large site for storing the modules close to the construction site (no more than 20 minutes away). The closer the modules are to the site, the more optimized the installation will be.
- Installing the modules in vertical phases (from the first level to the roof). This method allows for quicker progress and lets your subcontractors start their work on the already installed phases more rapidly.
Certainly! At the appropriate time, we can compare our prices, and if you still wish to, we can install your exterior doors and windows at the factory. It’s one less hassle for you on the construction site!
Yes, you can install concrete balconies on the site. We will plan the module structure accordingly and can install your anchors at the factory.
Certainly! We can adjust our compositions to meet your needs. For example, a soundproofing concrete layer can be added to our modules, which already have superior soundproofing compared to the standards required by the National Building Code. Our insulation also meets the strictest standards for remote areas as well as those required by Novoclimat 2.0. Inform us of your needs and we’ll be happy to address them!
Our UsiBloc construction system is suited for urban and nearby regions where there is a high availability of contractors, labor, and subcontractors. This allows you to obtain better prices for professionals such as building mechanics. For more information, we invite you to check the benefits of this method in the UsiBloc Construction tab.
The UsiNor system is designed for remote areas where labor is increasingly scarce. UsiNor modules include more elements such as building mechanics, drywall, and cabinets. Note that this type of construction needs to be planned early in your design phase and requires more pre-project coordination with your professionals.
The UsiNor system is designed for remote areas where labor is increasingly scarce. UsiNor modules include more elements such as building mechanics, drywall, and cabinets. Note that this type of construction needs to be planned early in your design phase and requires more pre-project coordination with your professionals.
We have been evolving for 20 years, and we aim to make our projects faster and more cost-effective overall. Our experience has led us to reevaluate the advantages and disadvantages of traditional and modular construction to leverage the strengths of both, considering the regions of Quebec and the available labour. We invite you to review the benefits of the UsiBloc construction method in comparison to traditional modular construction, which includes mechanics, drywall, and finishing.
It is possible, and also preferable, to contact us at the early stage of a project. We can offer our services for a modular feasibility study, preliminary sketch drafting, or coordination with your professionals.
We do not have in-house architects or engineers. Our team includes building technicians and architectural technologists. We collaborate with external professionals for the planning of your project.
We can suggest professionals who are well-versed in our company standards, or if you prefer, we can also work with your existing professionals.
Contact us and tell us about your projects! We look forward to a future collaboration!
We do not have in-house architects or engineers. Our team includes building technicians and architectural technologists. We collaborate with external professionals for the planning of your project.
We can suggest professionals who are well-versed in our company standards, or if you prefer, we can also work with your existing professionals.
Contact us and tell us about your projects! We look forward to a future collaboration!

